Velo3D, Inc., a leading metal additive manufacturing technology company for mission-critical parts, today announced Keselowski Advanced Manufacturing (KAM) has acquired a Sapphire XC printer to expand its additive manufacturing capabilities and joined the Velo3D Contract Manufacturer Network. The purchase is Keselowski’s first from Velo3D and it continues the company’s legacy of utilizing the most advanced manufacturing capabilities on the market to deliver finished, high-quality parts to its customers.
The Sapphire XC printer purchased by KAM is calibrated to print in a nickel-based superalloy that delivers oxidation and corrosion resistance at high temperatures. The alloy is commonly used in aviation, space, defense, and energy applications, all of which are key industries for KAM. The company purchased the Sapphire XC to unlock the ability to print much larger parts for its customers.
“Our customers are some of the most innovative companies in their industries and, as a result, they present some of the most complex manufacturing problems to solve—this is where KAM thrives,” said Brad Keselowski, Owner and Founder of Keselowski Advanced Manufacturing. “We are continually investing in new technologies to provide the highest quality finished parts, which starts with additive manufacturing technology but also includes quality precision machining to a finished part. With our established processes and team, we feel confident that our Sapphire XC will allow us to serve new industries by increasing the physical size of the parts we can deliver. This will be our first Sapphire XC but as demand for these parts increases, we can easily add more printers to our fleet due to Velo3D’s machine-to-machine repeatability.”
The Sapphire XC has quickly become one of Velo3D’s most popular products since its first shipment in Q4 2021. It can print parts up to 600mm in diameter by 550mm in height. It is also available in a 1-meter option called the Sapphire XC 1MZ. The regular Sapphire XC can easily be upgrade to a Sapphire XC 1MZ by swapping out its build module.
“With such extensive experience in engineering, simulation, and manufacturing mission critical metal parts, the KAM team is well equipped to put the full printing capabilities of the Sapphire XC to work,” said Dr. Zach Murphree, Velo3D Vice President of Global Sales and Business Development. “With an extensive client-base of innovative companies operating in many of the same industries we work with, Keselowski Advanced Manufacturing will see extensive utilization of their new metal additive manufacturing solution.”
Velo3D’s fully integrated solution greatly simplifies the additive manufacturing process and easily incorporates into standard manufacturing workflows. Because of the solution’s calibration and underlying manufacturing processes, Velo3D customers can more easily scale up production to meet demand for their additively manufactured products. This is made possible by Velo3D’s ability to eliminate many of the variables that are commonly found in conventional additive manufacturing solutions. For customers and contract manufacturers, it means they can easily add more printers to their fleets to meet production demands without extensive requalification of every part.
About Velo3D

Velo3D is a metal 3D printing technology company. 3D printing—also known as additive manufacturing (AM)—has a unique ability to improve the way high-value metal parts are built. However, legacy metal AM has been greatly limited in its capabilities since its invention almost 30 years ago. This has prevented the technology from being used to create the most valuable and impactful parts, restricting its use to specific niches where the limitations were acceptable.
Velo3D has overcome these limitations so engineers can design and print the parts they want. The company’s solution unlocks a wide breadth of design freedom and enables customers in space exploration, aviation, power generation, energy, and semiconductor to innovate the future in their respective industries. Using Velo3D, these customers can now build mission-critical metal parts that were previously impossible to manufacture. The fully integrated solution includes the Flow print preparation software, the Sapphire family of printers, and the Assure quality control system—all of which are powered by Velo3D’s Intelligent Fusion manufacturing process. The company delivered its first Sapphire system in 2018 and has been a strategic partner to innovators such as SpaceX, Honeywell, Honda, Chromalloy, and Lam Research. Velo3D has been named as one of Fast Company’s Most Innovative Companies for 2023.
About Keselowski Advanced Manufacturing
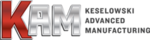
Keselowski Advanced Manufacturing (KAM) is a vertically integrated engineering through serial production advanced manufacturing company with additive manufacturing (LPBF-M) and Subtractive (CNC) capabilities. Our vertically integrated manufacturing strategy ensures the customer is with us every step of the way. We de-risk the additive manufacturing journey from start to finish with our end-to-end production solutions. From concept and design to manufacturing, post processing, surface finishing, assembly, and quality review – the KAM team collaborates to mitigate challenges and develop efficiencies, giving the customer complete visibility of their project throughout the process.